-
All-In-One Fiberglass Repair Kit
Shop Now and Start Your Repair! -
Featherweight Scissors
Shop NowLightweight, Durable, and Extremely Sharp. Gingher® Featherweights are versatile enough to tackle most jobs in the workshop.
-
Quart Mixing Set
Shop NowSimplify your project and let us gather supplies for you. This set contains what you need to mix one quart of resin and corresponding hardener.
-
Plastic Rollers
Shop NowThese Plastic Rollers are straight across the width of the head and provide excellent air relief for nearly all applications.
Fiberglass & Composites Overview
Composites offer numerous advantages over conventional building materials. One advantage that might not be obvious is the ease and durability of repairs. Because many lack the knowledge to repair composite parts and molds, damaged items are often replaced; for those that have a beginner’s understanding, the process may seem intimidating at first. Fear not, composite parts are often easier to repair than parts made from traditional materials. In this article we will provide a basic understanding of composite repairs, as well as detailed steps and considerations to follow for both structural and cosmetic repairs.
If you have landed on this article and have no previous knowledge of composite materials or the typical composites manufacturing processes, you might want to read some additional articles in our learning center. We have other articles that can help with some basic knowledge, including getting started in composites, the fundamentals of fiberglass, about resins, about reinforcements, and molding fiberglass. A broader understanding of composite materials and manufacturing methods, along with a little practice, can go a long way towards a more successful repair.
One point to get across prior to the heart of the article, we will use the terms composite repair and fiberglass repair interchangeably. This is because the techniques described will work for any fiberglass structure as well as many “advanced” composites made from Carbon Fiber and KEVLAR®. The overall concepts can be applied to most composite materials. That means we will provide you with the fundamentals for a wide variety of repairs—from cosmetic gel coat repairs, to intermediate boat and auto body repairs—all the way through structural composite repairs. One caveat, however, is that for certain parts, specialized procedures—beyond those described by this article—may be necessary. Manufacturers of highly technical or structural parts often publish detailed repair information specific to their parts. Our position is that the manufacturer’s instructions supersede all other information we provide and should be followed completely. Generally, manufacturer’s instructions are more specific and will not contradict the standard repair procedures outlined here. Caveat aside, when the fiberglass repair instructions in this article are well executed, strong repairs will result whether you are doing professional composites repair or diy fiberglass repairs.
What should I know about fiberglass repair?
There are a few fundamental principles that, once understood, allow most fiberglass repairs to be completed successfully. Successful repairs allow you to extend the life of a part or mold and save you the cost of replacing your composite part. Start by considering these three main principles of composite repair:
-
Repairs differ from the original part — The first principle you must understand is that structural repairs are made by a different process than the original piece. When a composite part is initially manufactured, its resin cures bonding both chemically and physically with the reinforcement fabric resulting in a single unit, regardless of the number or orientation of the plies of fabric. This is referred to as the primary structure or bond, and it is the strongest type of bond that can exist within a composite part.
Once a part is damaged, all repairs become secondary bonds attached to the original primary structure. This means all repairs are dependent upon physical bonding to the surface of the original primary structure (more on this later). For this reason, fiberglass repairs rely upon the adhesive quality of their resin for their strength—the strength of physical bond to the primary structure. Because of this, the resin used for the repair should be just as strong as the resin used to fabricate the part. In fact, resins with strong adhesive properties are sometimes used for repairs. -
Increased surface area will increase the strength of composite repairs — Since fiberglass repairs depend upon surface adhesion (physical bonding) of the repair to the primary structure, increasing the surface area of the bond line will increase the strength and durability of the bond—and by extension the part or repair.
Typically, the method employed to increase the surface area is taper or scarf sanding. This type of sanding means the area next to the damage is sanded away gradually, generally resulting in approximately ½—¾ of an inch of area per ply of composite laminate. Scarf sanding is usually done with a high—speed compressed—air power sander. Since most composite structures are fairly thin, this is a gentle process. The size of the taper, relative to the thickness of the laminate, is expressed as a ratio. Generally, the stronger or more critical the repair needs to be, the larger the ratio. Structural repairs usually require a gentler taper, with a ratio of 20:1 up to 100:1.
An alternative method employed to increase surface area is step sanding. This procedure defines the size of the inner repair, then removes surrounding materials at a width of ½" per ply of the part, working towards the part surface. This results in a considerable growth of the repair surface and allows the fiber orientation to be evident in each step.
Both methods are acceptable for the majority of composite repairs, though most consider scarfing to be easier, and it’s generally considered better. Stepping results in abrupt edges and butt joints in each repaired ply. It is also hard to step sand without cutting through, potentially damaging the underlying plies. -
You should match your fiberglass repair to the original part when possible — While your composite repair is different than your original part, it is recommended that you duplicate the thickness, density, and ply orientation of the original laminate when making your repair. This will help to maintain the functionality of the part. More is not always better—in this case, if your repair is thicker than the original part, it will almost certainly be stiffer, regardless of the material in use. Introducing various strengths within a part can cause unintended stress points, eventually leading to material fatigue or failure. It is better to carefully replace every ply that has been removed in the damaged area with an identical material, placed in the same orientation when possible. This ply—for—ply replacement approach guarantees the repaired structure can withstand the same loads as the original, and that it will disperse loads as intended.
With these three fundamental principles in place: Repairs Differ from the Original Part, Increased Surface Area Increases Strength, and Repairs Should Match your Original Part; you have the foundation for understanding the sequences for repairs. As stated earlier, we are going to provide detailed steps for both structural fiberglass repairs and general cosmetic composite repairs. Keep in mind that these are general steps, and certain applications may call for additional steps or slight variances in approach.
Steps for Structural Composite & Fiberglass Repairs
Since a structural composite repair will typically be followed by a cosmetic repair, we will start with the instructions for the more severe damage. In this section we will answer the frequently asked questions of "How do I repair fiberglass?" and "What do I need to repair fiberglass". This will be broken down into 4 steps:
- Inspect and measure, identify and determine
- Removing the damaged material and prepare the surface
- Laminate the repair patch
- Inspect the repair
Inspect and Measure, Identify, and Determine:
How to inspect damaged composites
There are four main categories for composite damage, your repair may involve one or all of these categories depending upon the severity of the impact or failure. The categories are as follows:
-
Tear
— This damage results when the tensile strength of the composite part has been exceeded and the laminate has failed. This typically results in a fracture which extends completely through the substrate.
- Hole or Puncture — This damage is typically a result of an impact or cutting. Holes and punctures are sometimes limited to surfacing layers or skins.
- Crushed Core — This damage applies only to composite parts containing sandwich core materials. It is typically the result of an impact which forces the composite skin of the laminate to deflect—but not fail—causing the sandwich core material to collapse.
- Delamination — This damage results in layers of the material separating from each other. It is typically caused by impact or stress between or across the layers.
How to measure the scope of your composite repair
Once you understand what type of damage you have, we recommend that you use a contrasting marker to outline the boundary of the damage. This will help you to understand the scope and magnitude of the damage, as well as offer you the chance to fully inspect your part. Take note, however, that you should inspect the damage carefully as the problem area often extends farther than can be easily detected visually. One inspection tip we can offer is the coin tap test. By tapping a coin around the surrounding area, you can quickly and easily generate an audible difference between a solid laminate, a crushed material, and a potentially delaminated area.
Is this repair worth the effort?
Once the extent of the damage and the type of material is known, you should determine whether the part in question should be repaired or whether you’re better off replacing it. If you’ve discovered the manufacturer’s specifications while you were identifying the necessary materials, check whether the damaged area is too large to be repaired. If no information can be reviewed, we recommend that you make a quick estimate of the materials and labor time needed for the repair. Compare this figure to the price of a new part. Typically, if you can achieve savings of at least 50 percent, you’ve met the cut—off to warrant proceeding with the repair.
Removing the damaged material and preparing the surface
Removing Damaged Material
Assuming you’ve already inspected the damaged area and marked it with a contrasting marker, you’re ready to begin removing damaged material. When a part is broken or crushed, it can be difficult to realign the pieces because frayed fibers tend to "hang up" on one another. In order to maximize the strength of your fiberglass repair, you will want to identify the sequence and orientation of the material as it is removed layer by layer. To help with this, use a saw blade to cut along the length of cracks or tears. This will relieve the stress on solid laminates, often allowing them to return to their original shape with little or no force. Parts constructed with a sandwich core material tend to pancake and mushroom, further complicating realignment. A router is excellent for removing damaged core material without disturbing intact face skins.
When removing damaged material, try to remove as little material as possible, so the scope of the repair does not grow larger than necessary. Be sure, however, to remove enough material to leave yourself with a solid laminate, which is necessary for a good repair. As you are removing damaged material, periodically stop and conduct another coin tap test. This will allow you to ensure you have removed all damaged material, and you should continue grinding or cutting away until all damaged material is removed.
Support the part and prepare the surface
After you’ve removed the damaged material, support the part so nothing is distorted during the repair process. Sometimes this is as simple as affixing a few strips of 2—inch wide masking tape, other times it is as elaborate as a custom-made clamping structure. Generally speaking, high—performance parts have tighter tolerances and will require a more precise support system. Once you’ve got the part supported, proceed with preparing the bonding surface. As mentioned above, this typically involves grinding or sanding a taper or steps in the material around the damage. This is the critical step for functional repairs, but it is also often overlooked or abused. Take your time and ensure your repair is performed correctly.
If a taper is to be used, measure the depth of the valley and calculate how far sanding must extend to achieve the desired ratio. Use your contrasting marker to mark the outer edge of your taper and begin sanding inward toward the valley. Be sure to remove material slowly so that the taper progresses evenly. As you expose each layer, write down the fabric type and orientation so that you can replace it in the same way.
When step sanding, the initial calculation is even more precise. For example, assuming the damage is circular, two inches in diameter and there are five plies in the laminate, mark concentric circles expanding one—half inch per ply from the edge of the innermost circle. The final diameter of the prepared area will be seven inches. Begin sanding in the center until the deepest layer is exposed. Step out one—half inch and sand down to the second deepest layer and so on, until all five steps are prepared. A right-angle grinder offers the best feel and control for this delicate procedure.
With either method, for personal safety and cleanliness, we recommend that you tape the hose of a shop vacuum to the work surface so that dust can be removed while grinding is taking place. Additionally, be sure that you wear a respirator and if possible protective clothing as this is a very messy process and you want to be as protected as possible. When sanding is complete, the whole surface must be cleaned thoroughly. Vacuum any remaining dust and then wipe the surface thoroughly with a solvent rag. Acetone is usually sufficient for removing oil, grease, dust, wax or other surface contaminants which could potentially interfere with your repair’s adhesion.
Helpful Products
Laminate the fiberglass repair patch
Prepare your composite patch materials
The first step to laminating the repair patch is pre-cutting your patch materials to fit the repair. This includes pre-cutting the core material and all reinforcement plies to fit within the taper you’ve prepared as you’ve readied the surface. If your part features a sandwich core material, cut the core first to fill the deepest hole. Note that some core materials, such as Nomex® Honeycomb, have their own orientation which needs to be aligned in the part. Be sure to check this for both sandwich core and reinforcement fabrics, consulting the list that was made during the preparation process so that each reinforcement ply is cut to fit in the proper orientation. Cut each ply so that it fits precisely into the area of the taper or into the step that was prepared for it. Modern repairs are made ply—by—ply, so the smallest piece is intended to go first, into the bottom of the valley. Stack the reinforcements near where they will be used, with the first layer to be placed in the bonding area on top of the pile.
Measure, mix, and apply your resin
Once your patch materials are prepared, pre—weigh the reinforcement schedule. You should target a 50:50 fiber to resin ratio for your repair, so once you have weighed your reinforcements, measure out the same weight of resin. Add catalyst or hardener and mix the resin as instructed.
Once you’ve measured and mixed your resin, start by pre—wetting the entire bonding area with resin. This will allow you to build a film of resin across the entire bonding area, maximizing the physical bond. Next you can begin saturating each ply of reinforcement before it is placed onto the part. Work on a sheet of plastic so the fabric can be easily lifted from the table once it’s ready. A flexible rubber squeegee is the best tool for spreading resin evenly through fabric and removing any excess resin which may be present. Place each layer of reinforcement into its spot on the repair, ensuring proper orientation.
Photo credit IStock Photo.
Stop every few layers to compact and debulk the patch as much as possible. The number of layers you can apply between debulking varies with the fabric weight and weave you are using, but typically you should debulk every 3—5 layers. A squeegee or fiberglass roller works well for this. Continue stacking the repair plies until all the fabric that was removed has been replaced. A final surfacing layer can then be added to cover the entire area. Plan on compacting the final repair patch as densely as possible while the resin is curing. The vacuum bagging technique is the most uniform method, but squeegees, rollers, or other clamping pressure will work adequately. Follow the manufacturer’s recommendations for curing the resin. If a two—sided repair has been planned, preparation for the opposite side can begin once the first patch has been fully cured, generally 48 hours.
Helpful Products
Inspect the repair
How to inspect a composite repair
Before you put your repaired part back into service, you need to inspect your repair. Use the coin tap method to inspect the repair after it has fully cured. The entire structure should resonate with the same solid sound. For more peace—of—mind or more critical parts, non—destructive load testing can also be implemented at this stage. This consists of stressing the part up to its expected service limit, but not beyond. If the part fails prematurely, even if the failure occurs away from your repair, it should be discarded. For more critical structures, a testing laboratory or specialized equipment may be necessary before sign—off.
If your part passes its inspection, you’re ready to proceed with the cosmetic repair.
Steps for Cosmetic Repairs
A part’s outer cosmetic finish is designed to hide and protect the structural reinforcement below, while also being aesthetically pleasing. It is this surface that most people will look at and judge the whole structure. Even slight damage like scratches and gouges will mar the finished appearance. Worse, these often create a direct path into the structural layers, causing even larger problems. Cosmetic blisters are a problem which, left untreated, can turn entire boat hulls into sponges.
The cosmetic composite repair sequence is similar to the structural sequence, but fairing and filling compounds and/or gel coat replaces the reinforcing material. Surface preparation is still the most important aspect of a long—lasting repair. Finish sanding and polishing present an additional step, but time invested on that step can result in a truly professional composite repair. Many people fear tackling cosmetic work because they assume it requires expensive spray equipment for satisfactory results. While equipment is important, proper material selection is the key to positive results.
In this section we will provide guidelines for cosmetic composite repairs, including fiberglass crack repair, fiberglass gel coat repair, and composite repair finishing. This will be broken down into 5 steps, which are similar to those required for structural repairs:
- Inspect, Measure and Identify.
- Removing damaged material and preparing the surface
- Mix and apply filler
- Polish the repair area
Now let’s dive into each of these in more detail.
Inspect, Measure and Identify
How to inspect cosmetic damage
Inspection of cosmetic damage is just as important as it is with structural damage. There are four main categories for cosmetic composite damage, and you may find one or all of these types of damage depending on what your part has been through. The categories are as follows:
•Gouge A gouge is a long, deep depression in the surface, severe enough to require filler and a surface coat for repair. Gouges are typically caused by rough handling, glancing impacts, or improper padding.
•Blisters Blisters are bulges appearing on the surface of a part. It is typically caused by liquid or gas that has gotten into the substrate, forcing the skin away from the glass.
•Scratches Scratches are similar to a gouge, but not deep enough to require filler. Scratches are typically able to be repair without the need for filler.
•Crazing Craze cracks are hairline fractures that do not go through the thickness of the part, sometimes they do not even go through the thickness of the surface coat. Crazing is typically caused by either over-stressing of the part, thermal issues, or stress between or across the layers.
How to measure the scope of your composite repair
Once you understand what type of damage you have, we recommend that you use a contrasting marker to outline the boundary of the damage. Note that gouges often leave undercut areas of unsupported gel coat which at first will appear to be fine. However, if you press on them with a blunt tool, they will easily crack away. It is critical that all damaged areas are fully identified so they can be prepared correctly in the next procedure. Once you have your areas identified and marked, determine the approximate surface area that requires repair.
How to identify composite repair materials
After you’ve successfully identified the size and scale of the cosmetic damage, you should be able to approximate how much repair material is required. Gouges and Blisters will require both filler and gel coat, while scratches and crazing can typically be repaired with gel coat alone. If your part was originally made with polyester resin, polyester filling compounds and gel coat are suitable for the repair. If you are unsure, we also offer epoxy fillers as well as Duratec® Surfacing Primer which will offer a surface that either epoxy or polyester can bond to.
Helpful Products
Removing the damaged material and preparing the surface
Removing the damaged material
For both gouges and blisters, you will need to be sure that unsupported surface material is removed. As mentioned previously, this can be accomplished by pressing on them with a blunt tool. Once unsupported material has been removed, wipe the surface with acetone and a rag to remove any wax, oil or grease which might contaminate the repair.
When the surface has dried, tape off the area surrounding the damage. This will keep sanding scratches to non—damaged areas to a minimum. Proceed by chipping out all loose material with a utility knife and then use 40—grit sandpaper to bevel the edges to a taper. Even thin cracks will have to be "opened up" before material can be added to fill them. Blisters will have to be completely exposed at this time. While you are expanding the damaged area, be ensure that the remaining laminate is solid and dry. If the laminate is not solid and dry, you may have additional structural repairs to complete prior to finishing your cosmetic repair.
Prepare the surface
After you’ve removed the damaged material and opened up the cracks, use a medium grit sandpaper to sand slightly into the surrounding area. This will give you the ability to feather your repair into the undamaged surface. After you’ve finished sanding the surface, wipe down the surface with acetone one final time to remove dust and anything else that may disrupt adhesion.
Helpful Products
Mix and apply filler
Filling shallow gel coat scratches and crazing
Shallow scratches can be directly filled with color matched gel coat rather than a filling compound. Be sure that you match your gel coat to a sanded and polished portion of the original, rather than the overall faded color. Your repair may stand out at first, but everything will fade to the same color in about a month. When using gel coat to fill a scratch, use a small brush to dab in the gel coat. Be sure it is higher than the surrounding surface so that it can be sanded flush. Spray a light coat of PVA over the repair for a tack—free, sandable cure.
Filling compound for deeper scratches, gouges and blisters
Deeper gouges will require structural repair putty to replace the missing material before the finish coat of gel coat is applied. Resin mixed with 1/32 inch milled glass fibers is an excellent structural putty. We also offer a variety of both polyester and epoxy—based fairing and filling compounds. Use a squeegee to spread your selected filler into the bottom of the gouge. Keep this filler slightly below the surrounding surface if gel coat is the intended topcoat. If painting, the filler can be level with the surface since paint adds little thickness. When filling blisters, such as in a fiberglass boat hull repair, be sure to use vinyl ester resin with your milled glass fibers to make your putty. This will add additional corrosion protection to these weakened areas.
If your cosmetic repair is following a structural repair, it may be necessary to level the structural patch with the solid laminate. Both grinding and filling may be necessary to accomplish this. Grind all high spots until they are flush with the rest of the surface, unless this will compromise the structural strength of the patch. Use filler to level any low spots. If grinding cannot take place for structural reasons, fillers can be mildly added to smooth irregularities and sanded to a smooth feather, but the patch will then always be visible. For marine repairs, use the 1/32 inch milled glass putty filler as described previously. Other structures can usually be filled with standard fillers or by mixing talc and a resin, unless otherwise specified. Continue adding filler and sanding until the surface is perfectly flush.
Epoxy repairs are quite stable once they are cured, but polyester repairs should be heated slightly before final finishing. Polyester resin in the repair patch and in standard body filler often continues to shrink for some time when exposed to heat. This can be avoided if you use one of our non—shrink polyester fillers, but otherwise simply place the project out in the sun for a few days or set up a heat lamp. If a lamp is used, however, don’t place the part too close or leave it for too long. You are trying to "force" the filler to shrink prior to final sanding and don’t want to distort your part. Once you’ve sanded to the perfect contour, your part is then stabilized against future heat problems.
Mix and apply the color—matched top coat
For a gel coat finish
If gel coat is the intended top coat, we would always recommend a sprayed application. We sell a variety of spray guns for the various sizes you might encounter on a repair, from a full—sized Gel Coat Cup Gun, down to our Preval Sprayer which can be used for the smallest repair. All of the gel coats we sell are formulated for application via spray gun, and this application method provides for the best surface finish. Specifically for repairs, we recommend you mix your gel coat with Duratec® Hi—Gloss Additive. This additive will allow for an open—air cure, thin your gel coat, and reduce orange peel. This means you don’t need to add wax that would require additional labor, your gel coat will be easier to spray, and you will have less sanding and polishing to finish your repair. For below—the—waterline repairs on marine projects it is recommended that you use a surfacing agent like PVA or Styrene Wax to ensure a thorough cure. Wax is excellent for large, hard—to—reach areas, but it can cloud clear gel coats. PVA is best used for spot repairs, or where access is easy while the gel coat is still wet.
Gel coat will need to be sanded prior to final buffing. Use a hard rubber sanding block and start with 400—grit wet/dry paper to level the gel coat. Focus the sanding effort only on the high spots until everything is flush. Then switch to a foam sanding pad and finer sandpaper for the perfect finish. Be sure to change the water each time you move to a finer-grit sandpaper so the dust particles from the coarser paper do not continue to cut the surface.
For a paint finish
If paint is your top coat, a surfacing primer is worth applying underneath. The primer will hide the fine irregularities that may still exist while also sealing the patch. For most repairs, Duratec® Surfacing Primer is the best material for the task. It has a high heat distortion temperature, which further protects already stabilized patches from shrinkage. Most paint systems will stick to cured epoxy, so be sure to check your paint for primer recommendations prior to use.
Helpful Products
Polish the repair area
How to finish a composite repair
The last step of a professional composite repair is buffing and polishing. Our #1102 and #1103 Mold Polishes are prefect for use with either polyester and epoxy patches or gel coat finishes. For polishing a paint finish, you will need only #1103, our Step 2 compound. These compounds will quickly remove the fine scratches left by 600—1000 grit paper while also removing overspray and some of the halo effect commonly left around spot repairs. The Step 2 polish will give your repair the high luster you want for your final shine.
What about SMC? How do I repair SMC?
Sheet molded compound (SMC) is a composite material that is frequently used in the automotive, industrial, and personal watercraft market. SMC poses unique repair problems, so we will discuss it briefly.
First, it’s important to recognize SMC as different from other types of FRP composites so that the proper repair can be performed. Parts made with SMC are typically produced in compression molds, causing them to be smooth on both the inside and outside—typically the first clue to identifying them. Next, SMC parts do not have an outer gel coat, rather they are typically color molded and sometimes painted. Finally, when the paint is sanded from SMC, short coarse fibers are exposed and the dust that is generated is dryer and more powdery than other composites. These hints will make it easier to identify SMC.
Next, you need to select the correct resin. While SMC is a polyester—based material, it cannot be repaired with polyester resin. This is due to there being a mold release agent present throughout the entire SMC part. Unlike conventionally molded parts, where release agents are applied to the mold surface, SMC is compounded with a release agent dispersed within the resin mix for faster processing. This means that as the damage is sanded to prepare a good bonding surface, fresh release agent is exposed. Polyester resin products do not offer a strong enough physical bond to adhere to this surface. Because of this, SMC should only be repaired using epoxy—based resins, fillers, and adhesives.
How do I finish an SMC repair? Most SMC repairs will be painted, and only catalyzed type paint systems should be used.
Summary
Composites are a growing category, gaining larger acceptance in all types of modern vehicles, structures, and recreational equipment. The more they are used, the more they will begin to fatigue and break; when the parts break, they do not all need to be replaced. By following these procedures, you can be confident enough to embark on simple repair projects. With a little practice, you can expand into more difficult tasks. This article is intended to help get anyone started. Whether you are working up the courage to embark on a fiberglass tub repair, a pool repair, or auto body repair, we this article can give you the fiberglass repair tips needed to get started. Practice will hone and improve your skill, but following these simple guidelines will allow you to achieve a positive result the first time.
In closing, be sure to remember these few keys to a successful repair.
- Start Smart: inspect the damage thoroughly, mark the damage clearly, identify what material the original part was made from, and decide if the repair makes sense.
- Preparation is key: The number one area that dictates the success of a fiberglass repair is the removal of damaged materials and proper preparation of the bonding surface.
- Plan the repair: Make your structural repairs ply-by-ply have your materials pre-cut and use the appropriate resin. For cosmetic repairs, have the appropriate materials on hand and don’t make more work for yourself than necessary.
- Inspect and finish: After you’ve made a structural repair, be sure that you inspect the part prior to putting it back into service. After you’ve made a cosmetic finish, spend the extra time to make sure it shines.
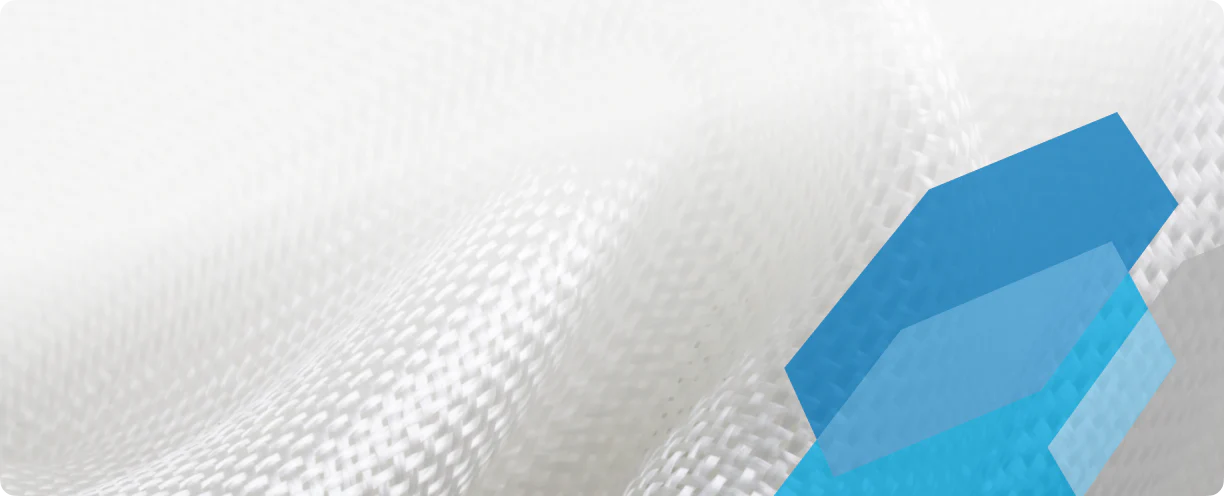